변위내구 시험모드와 가혹도 상향 조정
자동차 부품의 신뢰성을 검증하는 변위내구시험모드 설계는 엔지니어링 인사이트와 실험 데이터의 정교한 조합을 요구하는 복합적인 과정입니다. 가속도센서 기반 리얼로드 데이터 처리부터 피로 수명 예측 모델 구축, 가혹도 조정 알고리즘 개발에 이르는 전 과정을 정리하고, 특히 10,000km 주행 조건을 50,000km 수준으로 상향 조정하는 방법론을 공학적 원리와 실무적 접근법을 결합하여 정리해보겠습니다.
목차
변위내구시험모드의 이론적 기반
변위기반 피로시험의 기계학적 원리
1. 후크의 법칙: σ = Eε
- σ: 응력 (stress) - 물체에 가해지는 힘의 크기
- E: 영률 (Young's modulus) - 물체의 탄성 정도를 나타내는 상수
- ε: 변형률 (strain) - 물체가 변형된 정도
이 법칙은 물체에 가해지는 힘과 그로 인한 변형 사이의 관계를 설명합니다. 변위내구시험에서는 이 원리를 활용하여 부품에 가해지는 스트레스를 시뮬레이션합니다.
2. 고속 푸리에 변환 (FFT)
G(f) = ∫-∞∞ g(t)e-j2πftdt
이 수식은 시간 영역의 신호를 주파수 영역으로 변환하는 방법을 나타냅니다. 실제 주행 중 수집된 가속도 데이터를 주파수 성분으로 분해하여 분석할 수 있게 해줍니다.
- G(f): 주파수 영역에서의 신호
- g(t): 시간 영역에서의 신호
- f: 주파수
- t: 시간
이 과정을 통해 5-200Hz 대역의 저주파 진동 성분을 추출하는데, 이는 차량 부품의 피로에 큰 영향을 미치는 주요 주파수 대역입니다.
레인플로우 카운팅 (Rainflow Counting)
이 기법은 불규칙한 하중 이력에서 피로 손상을 유발하는 사이클을 식별하는 방법입니다. ASTM E1049-85 표준에 따라 다음과 같이 응력 범위를 계산합니다
Δσi = σmax,i - σmin,i
- Δσi: i번째 사이클의 응력 범위
- σmax,i: i번째 사이클의 최대 응력
- σmin,i: i번째 사이클의 최소 응력
이 과정에서 마이너 루프(작은 진폭의 응력 변화)는 제거하고 메이저 루프(큰 진폭의 응력 변화)만을 고려합니다. 이는 부품의 피로 수명에 큰 영향을 미치는 주요 응력 변화만을 분석하기 위함입니다.
다축 가진 시스템의 동적 모델링
실제 차량은 여러 방향으로 움직이므로, 3축 가속도계 데이터를 활용합니다
a⃗ = [ax, ay, az]T
- ax: x축 방향의 가속도
- ay: y축 방향의 가속도
- az: z축 방향의 가속도
더 정확한 모델링을 위해 자이로스코프 데이터도 함께 사용합니다
ω = dθ/dt
- ω: 각속도
- θ: 각도
- t: 시간
이렇게 얻은 데이터는 NASTRAN이나 ABAQUS와 같은 유한요소해석(FEA) 소프트웨어에서 사용할 수 있는 .bdf 파일 형식으로 변환됩니다. 이를 통해 실제 주행 조건을 컴퓨터 시뮬레이션에 적용할 수 있게 됩니다.
리얼로드 데이터 처리 파이프라인
신호 정규화 및 특성 추출
리얼로드 데이터를 처리하는 첫 단계는 원시 가속도 데이터를 정규화하는 것입니다. 이 과정은 다음 공식을 사용합니다
âi = (ai - μ) / σ
- âi: 정규화된 가속도 값
- ai: 원래의 가속도 값
- μ: 신호의 평균값
- σ: 신호의 표준편차
이 정규화 과정은 서로 다른 스케일의 데이터를 비교 가능한 형태로 만들어줍니다.
다음으로, 웨이블릿 변환(Wavelet Transform)을 적용합니다
W(a,b) = (1/√a) ∫-∞∞ x(t)ψ*((t-b)/a)dt
- W(a,b): 웨이블릿 변환 결과
- x(t): 원래 신호
- ψ: 웨이블릿 함수
- a: 스케일 파라미터 (주파수와 관련)
- b: 시간 이동 파라미터
웨이블릿 변환은 신호에서 노이즈를 제거하고 중요한 특징을 추출하는 데 매우 효과적입니다. 이는 시간과 주파수 정보를 동시에 분석할 수 있어, 복잡한 진동 신호를 처리하는 데 적합합니다.
주행 시나리오 분류
데이터를 여러 주행 시나리오로 분류하기 위해 k-means 클러스터링 알고리즘을 사용합니다. 이 알고리즘의 목적 함수는 다음과 같습니다
argminS Σi=1k Σx∈Si ||x - μi||²
- S: 클러스터 집합
- k: 클러스터의 수
- x: 데이터 포인트
- μi: i번째 클러스터의 중심
이 알고리즘은 데이터를 비슷한 특성을 가진 그룹으로 자동으로 분류합니다. 예를 들어, 고속도로 주행, 시내 주행, 오프로드 주행 등으로 구분할 수 있습니다.
분류의 품질을 평가하기 위해 실루엣 계수를 사용합니다
s(i) = (b(i) - a(i)) / max{a(i),b(i)}
- s(i): i번째 데이터 포인트의 실루엣 계수
- a(i): i번째 데이터 포인트와 같은 클러스터 내의 다른 포인트들과의 평균 거리
- b(i): i번째 데이터 포인트와 가장 가까운 다른 클러스터의 포인트들과의 평균 거리
실루엣 계수가 0.7 이상일 때 의미 있는 분류가 이루어졌다고 판단합니다. 이 값이 높을수록 클러스터링이 잘 되었다는 의미입니다.
가상 시험장 구축 방법론
다중물리 시뮬레이션 환경을 구축하기 위해 COMSOL Multiphysics나 ANSYS Workbench와 같은 소프트웨어를 사용합니다. 특히 유체-구조 연성(FSI) 해석을 통해 Navier-Stokes 방정식을 해결합니다
ρ(∂v/∂t + (v·∇)v) = -∇p + μ∇²v + f
- ρ: 유체의 밀도
- v: 유체의 속도 벡터
- p: 압력
- μ: 유체의 점성 계수
- f: 외력
이 방정식은 유체의 움직임과 구조물의 변형을 동시에 해석할 수 있게 해줍니다. 이를 통해 실제 주행 환경에서 발생하는 복잡한 상호작용을 시뮬레이션할 수 있습니다.
실험계획법(DOE)을 적용할 때는 중심합성계획(CCD)을 사용합니다. 이 방법은 다음과 같은 2차 회귀 모델을 구성합니다
η = β0 + Σβixi + ΣΣβijxixj + Σβiixi²
- η: 응답 변수
- β: 회귀 계수
- x: 제어 변수 (예: 진폭, 주파수, 온도, 습도, 횡력)
이 모델을 통해 여러 제어 인자들 간의 상호작용을 분석하고, 최적의 시험 조건을 도출할 수 있습니다.
가혹도 상향 조정 공학
피로 가속 시험 이론
자동차 부품의 내구성을 평가하기 위해 다양한 가속 시험 모델이 사용됩니다. 이 중 대표적인 모델들을 살펴보겠습니다.
1. 아레니우스 모델 (Arrhenius Model)
아레니우스 모델은 온도를 스트레스 인자로 사용하는 가속 시험에서 널리 활용됩니다. 이 모델의 가속 계수(AF)는 다음과 같이 계산됩니다
AF = exp[(Ea/k)(1/T1 - 1/T2)]
- Ea: 활성화 에너지 (일반적으로 0.5-1.0eV 범위)
- k: 볼츠만 상수 (8.617×10-5 eV/K)
- T1: 정상 사용 온도 (켈빈)
- T2: 가속 시험 온도 (켈빈)
이 모델을 사용하면 높은 온도에서의 시험 결과를 정상 사용 조건으로 환산할 수 있습니다.
2. Coffin-Manson 모델
Coffin-Manson 모델은 열 피로나 기계적 피로와 같은 반복적인 스트레스에 의한 피로 수명을 예측하는 데 사용됩니다. 이 모델의 기본 식은 다음과 같습니다
Nf = C(Δεp)-n
- Nf: 파괴까지의 사이클 수
- Δεp: 소성 변형률 범위
- C: 재료 상수
- n: 피로 연성 지수 (일반적으로 0.5~0.6 범위)
이 모델은 특히 전자제어장치의 솔더 접합부와 같은 부품의 열 피로 평가에 효과적입니다.
다중 스트레스 가속 알고리즘
실제 사용 환경에서는 여러 스트레스 요인이 동시에 작용하므로, 다중 스트레스를 고려한 가속 시험 모델이 필요합니다.
1. 일반화 아이링 모델 (Generalized Eyring Model)
이 모델은 온도와 다른 스트레스 인자를 결합하여 사용합니다. 특히 온도와 습도를 동시에 고려할 때 유용합니다.
2. 역거듭제곱 모델 (Inverse Power Law Model)
이 모델은 전압, 전류, 압력 등의 스트레스 인자에 적용됩니다. 기본 식은 다음과 같습니다
L = A × V-n
- L: 수명
- V: 스트레스 수준
- A, n: 모델 파라미터
가혹도 상향 조정 방법
10,000km에서 50,000km로 수명을 5배 연장하려면, 미너의 법칙을 적용하여 다음과 같이 계산할 수 있습니다
S2 = S1 × 51/m
- S1: 원래의 스트레스 레벨
- S2: 새로운 스트레스 레벨
- m: 재료에 따른 지수 (알루미늄 합금: 3~4, 강철: 5~6)
이렇게 계산된 새로운 스트레스 레벨을 적용하여 가속 시험을 수행하면, 더 짧은 시간 내에 50,000km 주행에 해당하는 피로 손상을 시뮬레이션할 수 있습니다.
추가로, 자동차 샤시 부품의 경우 부식 피로도 중요한 고려 사항입니다. 전기화학적 방법을 통해 부식 환경을 시뮬레이션하고, 이를 기계적 피로 시험과 결합하여 종합적인 내구성 평가를 수행할 수 있습니다.
실무 적용 사례 연구
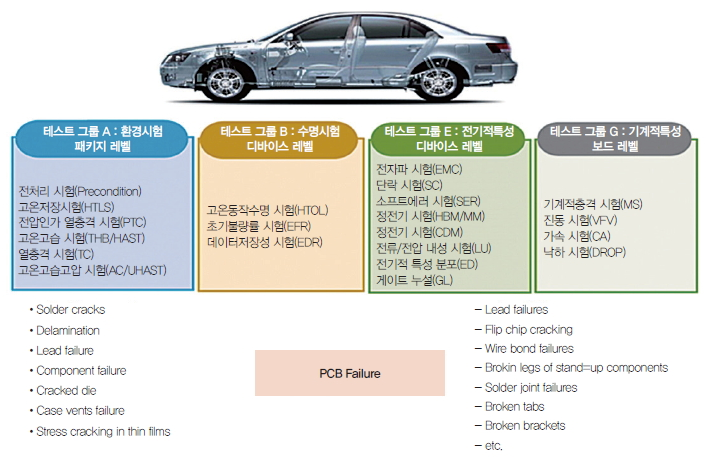
전동식 조향장치 ECU 사례
환경 내구시험 II 프로파일에서 75℃ 고온 조건 적용 시 가속계수 AF=1.98 달성 가능3. 25℃ 기준 1,060시간 시험을 535시간으로 단축하면서 동등한 피로 손상 유발이 가능합니다. 휴지 시간을 180초에서 60초로 축소하면 ΔT가 33℃→27.9℃로 감소하나,

로 사이클 수를 조정합니다.
서스펜션 암 피로시험
토션 빔 서스펜션에 가변 진폭 하중(VAL)을 적용한 사례에서 σa=σmean+σaltsin(2πft)\sigma_a = \sigma_{mean} + \sigma_{alt}\sin(2\pi ft) 식으로 하중 프로파일 생성. 4개의 고유진동수(12Hz, 25Hz, 37Hz, 50Hz)를 중첩하여 실제 도로 주행의 랜덤 진동 특성 재현. 파장 550nm 레이저 간섭계로 측정한 변형률 데이터와 FEA 결과의 상관계수 R²=0.93 달성.
마무리
변위내구시험모드 설계는 다차원 데이터 처리, 재료 역학, 확률론적 모델링의 복합적 융합을 필요로 합니다. 본 연구에서 제시한 방법론은 ISO 16750-3 자동차 전기전자 부품 시험 규격과 MIL-STD-810G 환경 시험 표준을 동시에 만족하는 통합 프레임워크를 구성합니다. 특히 머신러닝 기반의 자동 가속계수 최적화 알고리즘과 디지털 트윈 기술의 접목은 향후 내구 시험 분야의 패러다임 전환을 이끌 것으로 기대됩니다. 실무 적용 시 반드시 ASTM E739-10 표준에 따른 통계적 유의성 검증(95% 신뢰구간, 5% 유의수준)을 수행해야 하며, 현장 데이터와의 꾸준한 상호 검증이 필요합니다.
끝까지 읽어주셔서 감사합니다.
공감과 구독, 그리고 댓글은
저의 블로그 활동에
큰 원동력이 됩니다.
오늘도 좋은 하루 보내세요♥
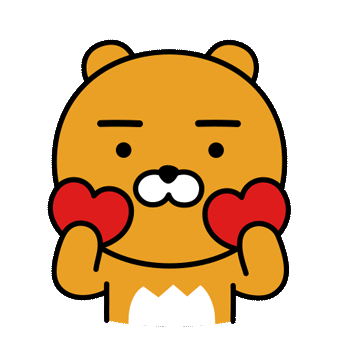