쇼트 피닝(Shoot Peening)의 유례
옛날의 대장간에서는 금속을 뜨겁게 만든 후 다 식을 때까지 햄머로 두들기는데, 이는 일종의 냉각단조 효과로서 오랫동안 전래되어온 비법이다. 이와 비슷한 효과를 갖는 공법이 쇼트 피닝으로 쇼트라고 불리는 작은 금속입자를 고속으로 제품 표면에 투사하여 작은 쇼트입자가 표면을 햄머링(Hammering)하는 공법이다.
미국이 1940년대에 이 공법을 기계공업 전반에 도입하였고 특히 자동차공업에 도입하여 일대 혁명을 가져왔다. 한편 일본은 이 공법에 대해 연구하던 중 태평양 전쟁에서 노획한 미국 자동차를 분해해봤고, 금속 표면에 미세한 압낭을 발견하였다. 이를 통해 쇼트 입자를 통해 제품의 재질을 단단하게 할 수 있는 쇼트 피닝 공법에 대해 알게 되었다.
50년대 일본은 한국전쟁 중 미군 자동차의 수리 또는 부품 제작을 미국으로부터 다량으로 수주받는 횡재를 통해, 미국 방산 분야로부터 여러 가지 제작에 대한 기술 지도와 노하우를 전수받게 되었다. 이를 통해 거의 모든 자동차 부품에 이론적 뒷받침을 제껴둔 채 실제산업에 쇼트 피닝 공법을 도입하게 되었고 이후 학계, 산업계가 이를 뒷받침하는 이론이나 연구에 착수하기에 이르렀다.
우리나라는 70년대 초반에 주물 청정용으로 쇼트 블라스트 기계가 도입되었는데, 이 때문에 쇼트 블라스트 공법은 주물공장에서만 사용되는 것으로 알게 되어 쇼트 블라스트 기계의 분류가 주조설비에 들어가게 되었다. 70년 후반에는 주강의 녹 제거(descaling)를 위한 용도로도 사용하게 되었으며 쇼트 피닝 용으로는 스프링 회사에서 사용하기에 이르렀다.
80년대엔 우리나라 자동차 부품에는 스프링을 제외하고는 거의 쇼트 피닝을 하지 않았다. 그러다 자동차가 해외 수출이 본격적으로 진행되었고, 여러 품질 클레임 발생에 따른 외국 기관의 조사가 진행되었다. 외국 기관은 해당 문제 부품을 쇼트 피닝 하지 않는 것이 원인으로 규명하였고, 이에 대응하기 위해 완성차 메이커사와 부품사들이 쇼트 피닝 고법에 대해 연구하고 적용하기 시작했다.
쇼트 피닝(Shoot Peening) 공법 원리
쇼트 피닝이란 작은 구형의 금속입자를 고속으로 발사시켜 금속표면에 충돌시키고 얻는 냉간 단조공법이라 정의할 수 있다. 좀 더 구체적으로 설명하면 쇼트의 입자는 E=1/2mV²의 운동에너지를 갖고, 작은 망치 역할로 금속표면을 강타하여 순간적으로 국부적인 발열을 일으키고, 표면에 박히며 국부적인 항복점을 넘게하여 소성변형을 준다.
쇼트와 충돌한 표면층 바로 아래층은 항복점에는 도달하지 않았으므로 강성은 유지하게 된다. 이 아래층은 표면층을 늘어나기 전의 상태로 유지 할려는 힘이 작용하고 표면에는 잔류 압축 응력, 내부는 인장 응력을 갖게 된다. 이 표면의 잔류 압축 응력은 내부 인장응력의 수배의 크기에 달한다.
일반적으로 부품에 응력이 가해지면 표면에는 인장응력이 가해지는데, 이 때 잔류 압축응력이 조금씩 상실하게 되고, 이에 따른 쇼트피닝 효과로서 피로강도가 상승하게 되어 부품의 수명도 증대시키게 된다.
벤딩이나 트위스팅 되는 부품의 피로수명을 연장시키는데 탁월한 효과가 있으며, 축방향의 인장/압축 응력에 대해서는 큰 효과가 없다. 축방향 인장력만 맞는 볼트에선 효과가 적으나, 하중 또는 진동을 받아 생기는 트위스팅 또는 벤딩 응력에 대해서는 효과가 있다.
끝까지 읽어주셔서 감사합니다.
공감과 구독, 그리고 댓글은
저의 블로그 활동에
큰 원동력이 됩니다.
오늘도 좋은 하루 보내세요♥
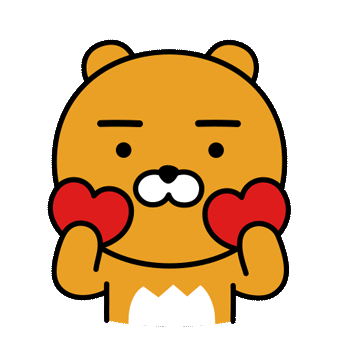
금속 열처리 기술과 종류별 열처리 방법
1. 금속열처리 1) 열처리 기술의 개요 열처리기술은 금속재료, 기계부품, 금형공구의 기계적 성질을 변화시키기 위하여 가열과 냉각을 반복함으로써 특별히 유용한 성질(내마성, 내충격성, 사용
sugarlessgum.tistory.com
[금속] 재질 기계적 성질(항복강도/연신율) 비교
[금속] 재질 기계적 성질(항복강도/연신율) 비교 구분 재질 두께 기계적 성질 브리넬 경도 규격/ 제조사 기호 등급 연신율 (%) 항복강도 (N/㎟) 인장강도 (N/㎟) HBW 열간 압연 강판 및 강대 KS D 3501 SPH
sugarlessgum.tistory.com
[자동차] 프레임과 차체 종류
[자동차] 프레임과 차체 종류 프레임은 섀시를 구성하는 각 장치와 바디를 부착하는 골격으로서, 부착된 부품과 바디로 부터 전달하는 하중, 전후의 엑슬로부터의 반력을 지탱해주는 중요한 부
sugarlessgum.tistory.com
금속(Metals) 경도 환산표
금속 경도 환산표 (Hardness Conversion Table for Metals) Steel Rockwell Rockwell Superficial Vickers Brinell Shore 인장강도 HRA HRB HRC HRD 15N 30N 45N HV HB HS Kgf/㎟ {N/㎟} 60Kgf 100Kgf 150Kgf 100Kgf 15Kgf 30Kgf 45Kgf 50Kgf 3000Kgf JIS 85.6 6
sugarlessgum.tistory.com
재질별 KS 규격, JIS 규격 비교, KS 재질규격
KS 규격 검색(E나라 표준인증) 바로가기 e-나라 표준인증 standard.go.kr KS 규격 KS 규격은 대한민국의 국가 표준화 기구인 한국표준협회(KS)에서 제정한 표준화 규격을 의미합니다. KS 규격은 다양한
sugarlessgum.tistory.com